News
Signode Creates Solution for Cargill
July 03, 2019
Cargill Malt provides malt bags and totes for the craft beer and whiskey industry. In the past, slick malt bags were stacked on a pallet, then banded to the pallet with a slip sheet and shrink-wrapped multiple times. 1,200 lb. malt totes were also banded the same way. Challenges to this method included load instability or compromised loads with product damage, as well as the expense of multiple consumables for palletizing.
To solve these problems, Cargill combined Signode's LOCK-n-POP® adhesive with a Muller stretch wrap, eliminating the need for slip sheets and banding, as well as reducing stretch wrap usage by 50%.
By switching to this solution, Cargill saw a $75,000 savings in raw materials costs. And according to Eric Hanson, Plant Manager in the Sheboygan, WI location, the 50-pound bags of malt grain can now be ordered in different quantity variations, based on the customer's need.
Says Hanson, "For us it was a cost savings to utilize this. We wouldn't use as much shrink-wrap to hold together the bags during transport. Plus, it gave us the ability when we pick an order for a customer, to pick one bag or five bags or a whole pallet, it just depends on what they're looking for. So, with the LOCK-n-POP®, it helps us with our organizational skills in the warehouse. It's a great product."
LOCK N' POP® is a non-toxic, water-based adhesive that secures packages together from the inside out. It is also approved by the FDA for indirect contact with food. By stabilizing the inherently slick bags from the center of the load outward, the shrink-wrapping process also becomes more effective. The bags then "pop" apart during unloading, without damage to the product.
Muller's stretch wrap uses proprietary resins that produce "superior strength and stretch" along with a high level of puncture resistance, requiring fewer wraps necessary for maximum strength.
Hanson says Cargill tested for a month or two before committing to the new system, then they had to "retrain workers to let the LOCK-n-POP® do its job." They have been using it for about a year, and Hanson says, "we have had really good results. We have heard and seen an improvement with our customer's satisfaction."
There are other added benefits to the new system, such as more efficient use of warehouse space since the pallets can now be stacked three-high and there is no longer a need to store banding and corrugated slip sheets. Fewer raw materials used in the packaging application improves sustainability, and Muller stretch film comes in taller rolls for a greater savings in wrapping.
View the article on the Packaging World website here.
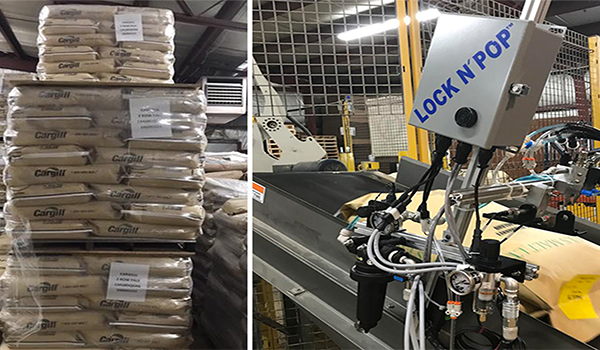